Color
Chart
Walk
doors are available in 3', 4' and 6' wide versions. If you leave
it up to us, we will install it right hand out for security. If you
want for it to swing in like in a typical home we will do it and we
will even accommodate the lefties.
French Doors are not often equated with metal buildings.
However most people would be surprised at how many we have installed
over the years. They let in a lot of natural light and really class
up a building.
Windows made right here in Arkansas come in many sizes. The
3030 size in white are the bargain of the group. 3030 stands for 3
feet 0 inches wide X 3 feet 0 inches tall. They are available in
lots of different sizes and colors. Best of all we know how to
install them so they don't leak. We don't use the old simple "J"
trim around our windows. Just about all windows with "J" trim will
leak during their lifespan. We use a system that was pioneered by
one of the real expensive national brands. It is a much better way
of trimming out windows on these metal buildings.
Attic Trusses are economical and give the customer the
opportunity to create a old fashioned attic in their new building.
Just to clarify the attic truss is not a attic. It is just a truss
that has been engineered to create a attic. Most customers create
their own attic by laying down the deck themselves. The big indoor
lumber yards carry the fold down stairs that most customers install
for the access.
Scissor Trusses are used in a building to create a cathedral
ceiling effect. Scissor Trusses give more interior height in the
center of a building. A scissor truss can be used to create a
dramatic interior if being finished out. A scissor truss can also be
used to lower the overall height of a building and still get a big
door in the end of it. This often comes into play when you don't
want the building to overwhelm the customer's home.
Gambrel Roofs are ancient and first appeared in America in
the 1774 Boston Carpenters price book. By having two different roof
pitches on the same roof makes the gambrel stand alone. Gambrel
Roofs are available in standard trusses, attic trusses and even
scissor trusses.
Insulation is standard with Ozark Metal Building. We feel so
strongly about this the customer will have to make a special request
to have it removed from a quote. Any enclosure will sweat once there
is a temperature difference between inside and outside more than 25
degrees. Insulating these metal buildings stops that. If a metal
building is not insulated the sweating(water dripping from the
ceiling) is inconvenient in the short term and a real problem in the
long term. Sweating will shorten the lifespan of a building. Ozark
Metal Buildings is in business for the long term. We do not want to
build something today that becomes a legacy cost in the future.
Furring Walls We can build Furring Walls for you on the
inside of the building so you can hang sheetrock. Furring
walls are built on the inside of the exterior walls inside
Pre-Engineered Steel Buildings and Post Frame Metal
Buildings so you have a smooth surface to screw(attach) your
sheetrock or tongue and groove wood siding to.
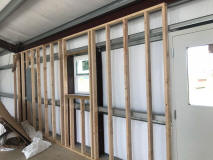
Internal Walls are essentially bedroom and bathroom
walls" These are built in such a way they are ready for you
to hang sheetrock. The internal framed openings for walk
doors are part of the package. We can also do "pocket doors"
if we know in advance."
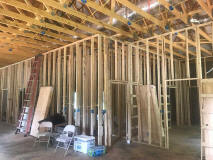
Internal Insulation is the second layer of insulation
(fiberglass batts) that is put in between the wall studs on
the exterior walls. All OMB buildings come with a R-10 value
and Low-E insulation installed sandwich method (this is done
so the building will not sweat). When the building is going
to be a home the R-10 is not enough. A second layer of
insulation is needed on the inside of the exterior walls. We
recommend and install fiberglass batts insulation as shown
in this photo. This second layer of insulation can be had in
R-19, R-24 and even R-30 values.
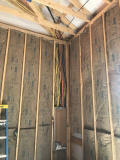
We like to quote the internal work only after we have
quoted the "shell" and you have acknowledged that this is
what you want.
Wood Corbels really soften up a metal building
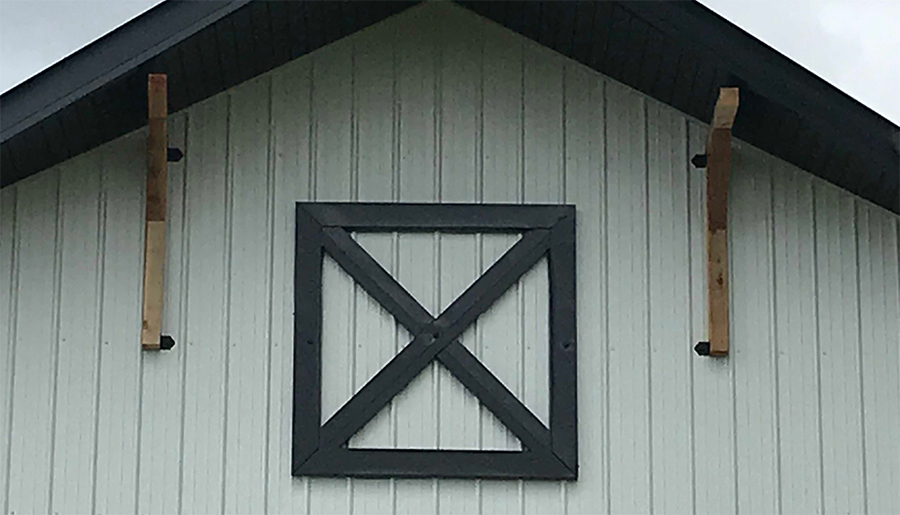
Stained Concrete
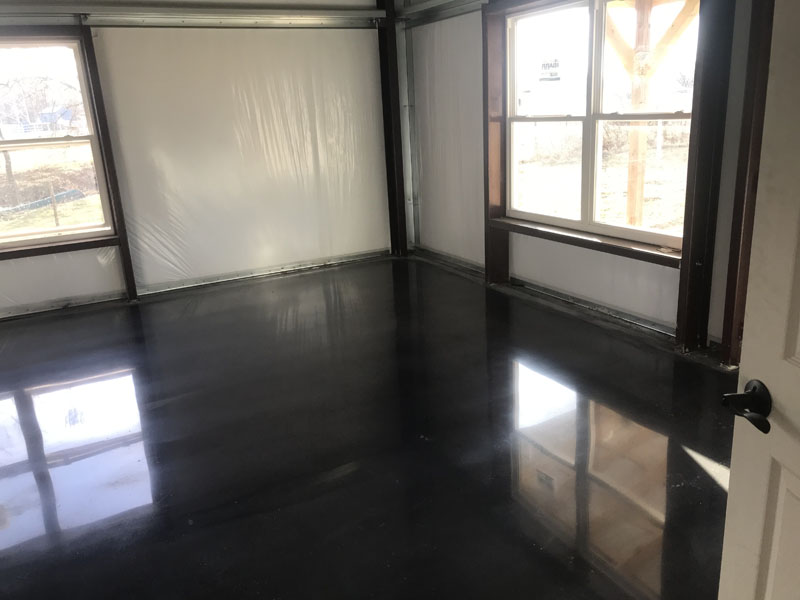
Cupolas add character. If you want for your building
to stand out from the crowd, a cupola will do it. Available
in different sizes to match the proportions of your
building. They come in maintenance free metal or glass. Past
customers have put lights inside their glass cupola's to add
a touch of whimsy.
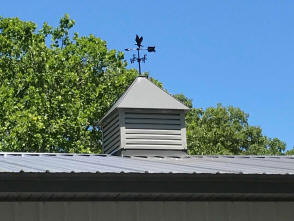
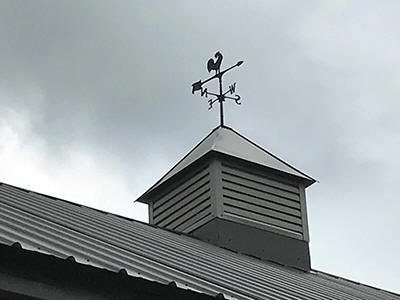
_small.jpg)
HVAC
Heat Ventilation Air Conditioning
systems are available. The hvac system is typically put in
before the internal walls and before the sheetrock is hung.
The size of the AC unit will be matched for your internal
volume.
Wainscot has been dressing up buildings since the
17th century. Wainscot is available in metal panels of a
different color. Wainscot comes with a special trim that
directs water to the outside of the building. (where it
belongs) It is also available in brick or stone, cultured or
real. We are fortunate enough to have a bricklayer with over
30 years of experience work for us. We usually can match
your homes existing brick or rock work. By using the exact
same brick or rock wainscot as your home, it instantly makes
your new building belong.

In-floor radiant heating systems
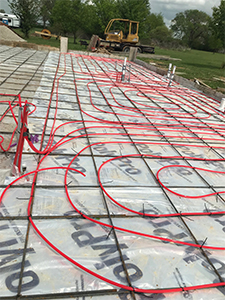
Dog Door
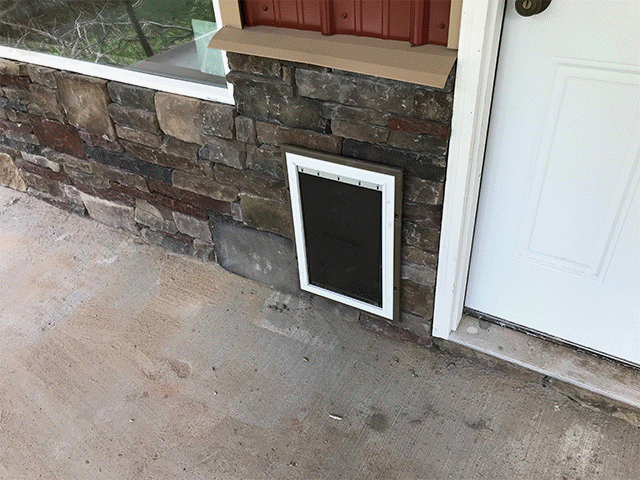
Custom Features - We offer a host of custom features
to make your building your own.
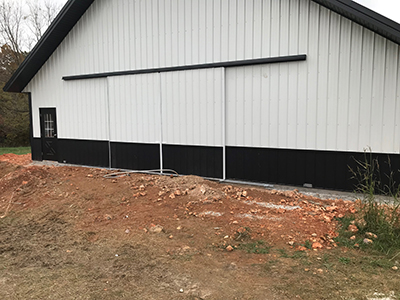
More information
Building Codes - vary from state to state, county to county
and city to city. Ozark Metal Buildings is a General Contracting
firm in good standing. Rest assured that your building will go up in
a timely manner, for the agreed upon price and without complication.
Permits - Ozark Metal Buildings usually pulls the permits for
the customer if it is standard. We pull it and the customer pays for
it.
Non Standard Permits - Some customers need a variance in
order to get a permit. Ozark Metal Buildings will advise and attempt
to pull a non standard permit. Please understand that securing a
building permit is not guaranteed.
Large Scale Development - If your project falls into Large
Scale Development we can help with that. By working with building
officials, architects, engineers and fire marshals we can push as
hard as anybody else can push. Please understand that LSD takes time
and money. Call the office for a consultation and fee schedule.
Termite pre-treatment is mandatory for a wood framed building
in Benton county and a good idea everywhere else. We include the
termite pre-treatment on all of our jobs for free. If you have an
existing termite contract with your home you can use the same
company at your expense. We will alert you to when they need to hit
the jobsite so it is seamless.
Ozark Metal Buildings practices performance pay points. When you
place a order with us we ask for a deposit. This initial deposit is
the only time you actually have to trust us. Every other pay point
comes after we have finished a portion of your building project.
Typically we ask for a partial payment after the dirt work is
complete. (if needed) Typically we ask for a partial payment after
the building kit has been delivered to your jobsite. We then
typically ask for a partial payment after the concrete floor has
been finished. Typically we ask for a partial payment after the
trusses are standing. We usually ask for the last partial payment
after the walk around.
The walk around is for the customer's security. A walk around is
where the customer and a representative of Ozark Metal Buildings
goes through that building making sure everything promised has been
completed. We make sure the windows work, make sure the overhead
doors seal up, make sure the trim looks strait. By not getting paid
the last portion until the punch list has been punched ensures the
customers satisfaction. This is the best way a customer can make
sure his or her building has been completed. A walk around is not to
renegotiate the price of the building nor is not intended to extract
a pound of flesh. We are reasonable people and ask the same from our
customers.
Terminology
Foundation vs Floating slab. It is common for any kind of
cement floor to be called a foundation. That is not always correct.
OMB wants for it's customers to know what they are getting for their
money and for there not to be any confusion. A foundation includes a
footer that goes below frost depth. Here in the Ozarks our frost
depth usually runs 16" to 18" deep. By getting the footer down below
the frost depth, it eliminates the heave from frost in the ground.
This stops the floor from moving up and down between winter and
summer.
Having a real foundation is required inside some city limits if you
want to add a bathroom. It is not required in Benton, Madison,
Carroll, Washington, Delaware or McDonald counties. However it could
be a requirement depending on what city the building will be built
in.
A foundation can be used with a Stick Frame Metal Building, a Red
Iron Metal Building or a Simple Home.
Floating Slab. A floating slab is not a foundation. A
floating slab does not have the footer. A floating slab moves up and
down about 3/8 of a inch between summer and winter. This movement
comes from moisture in the ground freezing and causing heave. Don't
let this brutal description scare you away from a floating slab. To
put it in perspective about 60 million homes in America are built on
floating slabs. They work just fine. We just want for our customer
to know what they are getting for their money. A floating slab is
used in Post Frame Metal Buildings. (Pole Barns) A Post Frame Metal
Building does in fact have a foundation, it is the big wooden post
going three feet in the ground. This simple but effective design is
what makes a Post Frame Metal Building so economical. This small
movement is imperceptible to the average user and does not affect
the utility of the building in any way.
Floating Slab with thickened edge. A floating slab with a
thickened edge around the perimeter is used on Stick Frame Metal
Buildings. Being that the outside perimeter walls are load bearing
on a Stick Frame Metal Building we give the slab extra concrete and
add in re bar around the outside perimeter. Though this is not
absolutely necessary, and some other companies do not add this, OMB
is in the business for the long run. It is so much less expensive to
build a building right the first time, than to try and repair it
later.
Concrete Block Wall Foundations are commonly used when
building on the steep terrain around Beaver Lake. Go ahead and point
to a steep hillside covered with trees, OMB can place your building
where you want. Once a hillside is over about 15% grade a
traditional red dirt pad no longer works. To combat this we excavate
a trench footing that contours to the slope. We make it contour by
adding in steps. This step footing will include the appropriate
amount of re bar held in the proper position using chairs. This step
footing will also include re bar uprights going into the blocks. We
then block up. Typically every seven layers of blocks get a bond
beam. A bond beam is a continuous layer of block that has re bar ran
through it horizontally. This adds additional strength. Depending on
the size and height the foundation may get a dead man anchor. A dead
man anchor is a glorified blob of concrete inside the foundation
that we use to pin to the bond beam. At the top of the block wall we
use what is called "L" blocks. L blocks are used to hair pin the top
of the block wall to the interior of the concrete floor. Each block
will have re bar ran through it vertically. All blocks are core
filled with a special concrete slurry to add strength. The interior
of the block wall foundation is back filled with rock. This
description is typical of a concrete block wall foundation. This may
seem like over kill by some, however it is the only way to be sure
that the foundation does not become a liability in the future.
Concrete Block Wall Foundations are used for Stick Frame Metal
Buildings, Red Iron Metal Buildings and Simple Homes.
Thoughts on Concrete
Here at Ozark Metal Buildings we understand concrete. If the sun is
shinning, or if it is cloudy. Summer vs Winter pours. Whether air
needs to be added because it will be a driveway or none for a
buildings floor. If we need to put a sprinkler on it to cool it down
or if we need to put straw on it to insulate it so it sets up.
Whether or not to add Calcium, and if so one or two percent
solution. Hot water to be added at the last minute or none. Keeping
the control joint sections small enough. Timing the saw joints so
the saw doesn't rip out the rocks because it is still too green and
not too cured that it already has a mind of it's own. The distance
between the batch plant and the job site also has to be accounted
for. If the air temperature is rising or falling. Humidity and the
cure time. Lots of calculations go into getting the customer a nice
floor finish that he or she will be proud of. When pouring concrete
nothing is a substitute for experience. In the past we have had
great results. However there is still a chance that the concrete
could crack outside the control joints. If it does happen there is
no structural damage, it does not weaken the floor. It's just not as
pretty as it could have been. We will give a sincere apology but no
money back. We take all known precautions and follow the same
formula that has worked in the past. We want our customers to know
that we are striving behind the scenes to get the best results
possible.
Ozark Metal Buildings is locally owned and operated. We are a debt
free company. We are proud of the buildings we build. We strive to
make every customer happy with their purchase. This leads to repeat
and referral business.
Financing is available through a third party.
Scott Yarbrough - General Contractor Owner
Architect
If you plan to build a residential building over 2000 square feet
you may be required to have an architect prepare drawings to get a
building permit. We recommend David Cox.
David S. Cox, AIA, CSI, CCS
Architect, Certified Construction Specifier
www.davidcoxconsultants.com
479-799-9920
david@davidcoxconsultants.com
"I think a lot of architects don’t understand that most clients want
a building that is affordable and meets their needs. I prefer to
focus on those areas rather than spending their money trying to
impress others with how clever a designer I am. David Cox"
|